Gas Turbine Combustion Chambers
Gas Turbine Combustion Chambers : Design, Function, and Challenges
Kian Turbo Tec is your trusted partner for gas turbine combustion chamber services, offering expertise in maintenance and overhaul to maximize efficiency and minimize emissions. Our commitment to quality and service excellence ensures your combustion systems perform optimally. Contact us to discuss how we can enhance your gas turbine operations.
Gas turbine combustion chambers are critical components in power generation and aviation systems, responsible for converting chemical energy from fuel into thermal energy through controlled combustion. Their design directly impacts turbine efficiency, emissions, and operational reliability. This article synthesizes key principles and modern advancements in combustion chamber technology.
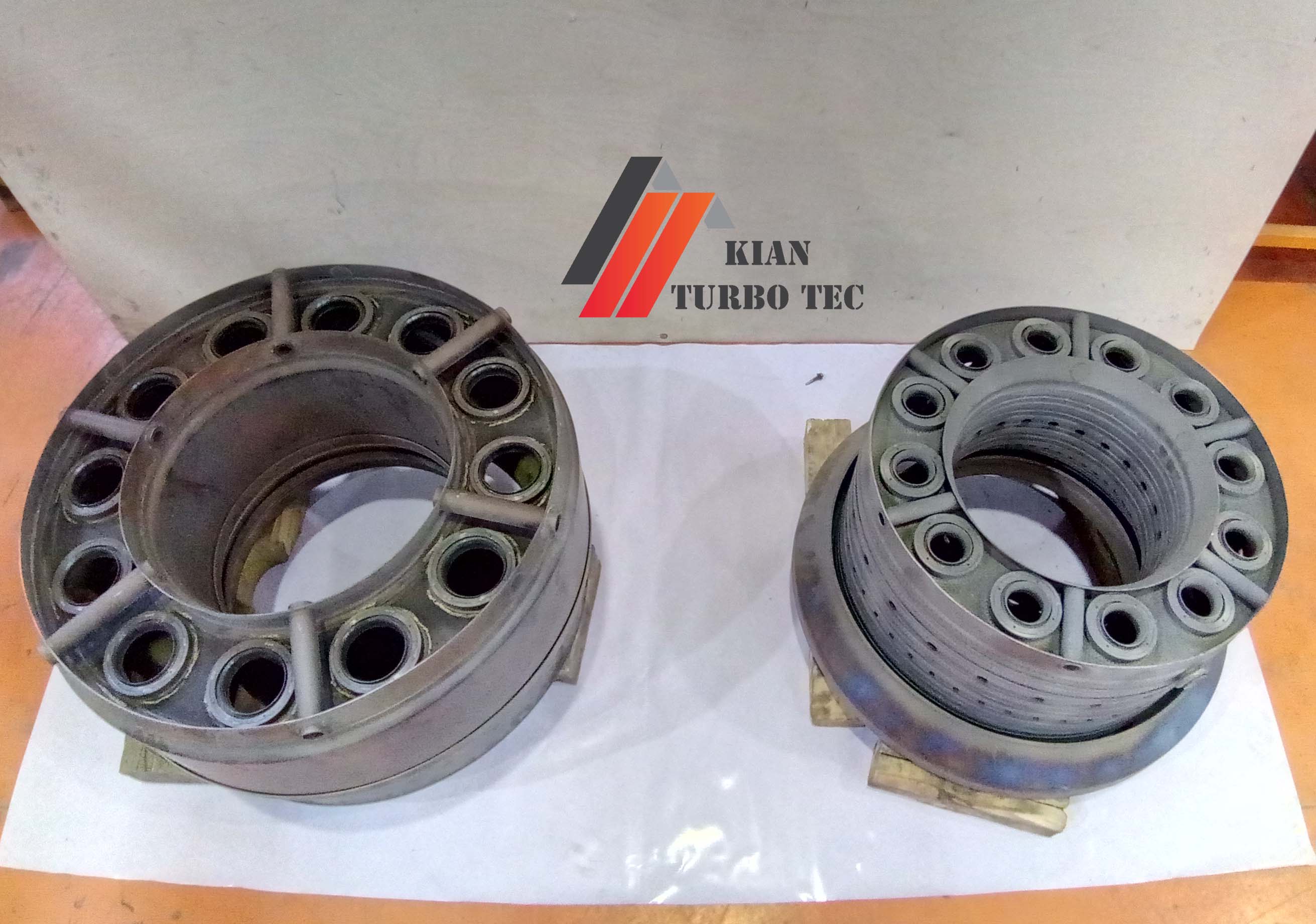
Figure 1 Combustion Liner of Taurus 70 Gas Turbine in Kian Turbo Tec workshop
Core Design Principles of Combustion Chambers
Combustion chambers are engineered to balance three competing demands:
- Efficient fuel combustion
- Uniform temperature distribution at the turbine inlet
- Minimal pressure loss.
To achieve this, modern designs follow two foundational principles:
- Zonal Division: The chamber is divided into a combustion zone (where fuel-air mixing and ignition occur) and a mixing zone (where dilution air ensures uniform exhaust temperatures). This separation prevents localized hotspots that could damage turbine blades.
- Airflow Management: Approximately 20-30% of compressor air is used for combustion, while the remaining 70-80% cools the chamber walls and dilutes exhaust gases.
Types of Combustion Chambers
Three primary configurations dominate gas turbine applications:
-
Annular Combustors:
– Annual Combustion Chambers Feature a continuous, ring-shaped liner encircling the turbine shaft.
– Offer compact design and uniform temperature distribution, making them ideal for aircraft engines.
-
Can-Type Combustors:
– Can-Type Combustion Chambers Consist of multiple cylindrical “cans” arranged around the turbine.
– Allow easier maintenance but create less uniform exhaust patterns.
-
Can-Annular Hybrids:
– Can Annular Hybrid Combustion Chambers Combine modular cans with an annular casing to balance maintenance accessibility and performance
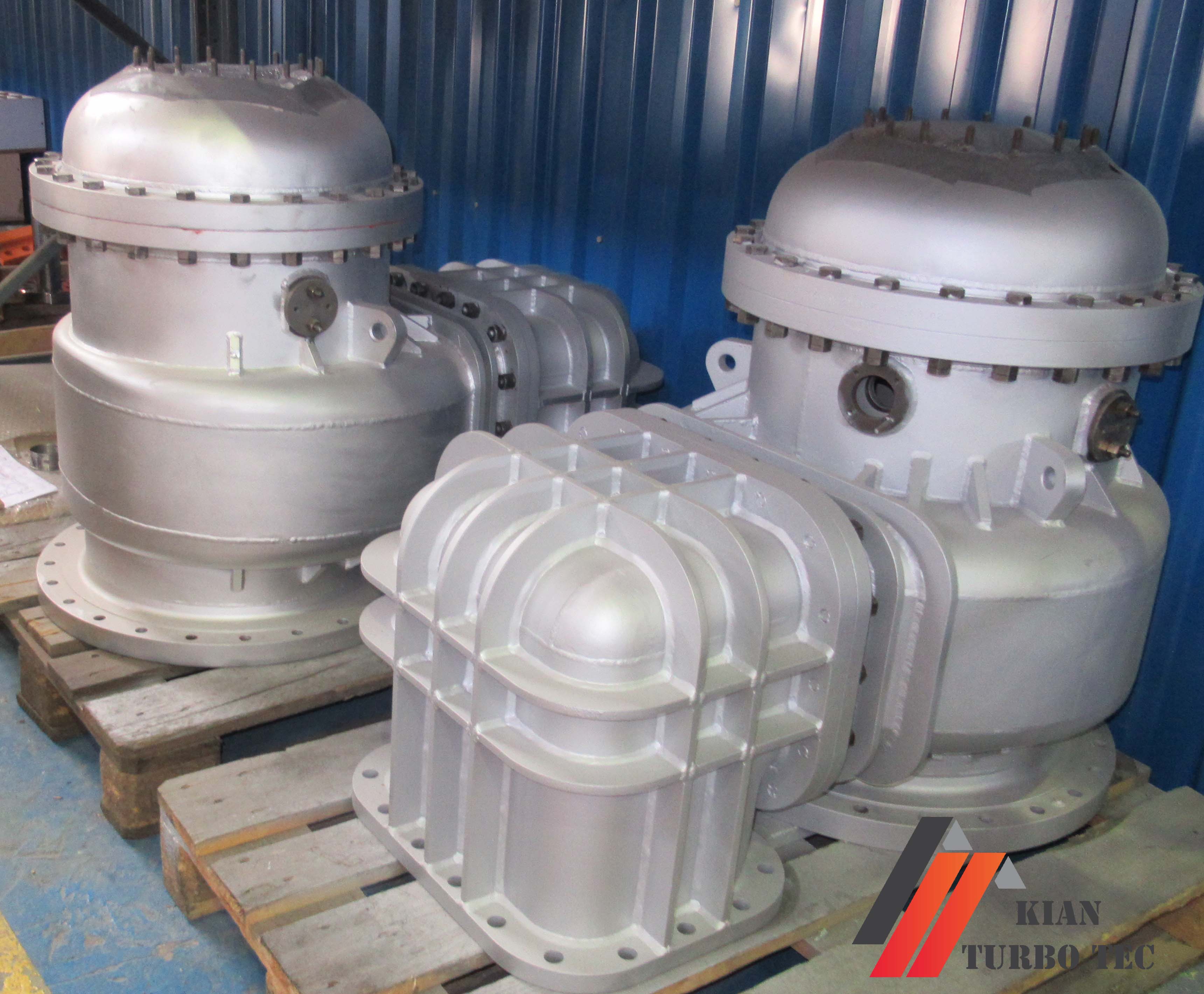
Figure 2 Chamber and Inlet Elbow of THM 1304 Gas Turbine, Overhauled in Kian Turbo Tec workshop
Key Functional Requirements for Combustion Chambers
- Stable Combustion: Must sustain flames across varying loads and fuel compositions.
- Emissions Control: Advanced chambers use lean-premixed combustion to reduce NOx by limiting peak flame temperatures below 1,800 K.
- Thermal Durability: Ceramic thermal barrier coatings (TBCs) protect metallic liners from temperatures exceeding 2,000°C.
Modern Challenges of Combustion Chambers
- Alternative Fuels: Hydrogen and synthetic fuels require redesigned fuel injectors to prevent flashback and autoignition.
Additive Manufacturing: 3D-printed swirlers and liners enable complex cooling geometries but face certification hurdles.
- Pressure Gain Combustion: Experimental designs like rotating detonation engines promise 10-15% efficiency gains but struggle with mechanical stress.
Future Directions of Combustion Chambers
Emerging computational tools like Large Eddy Simulation (LES) are refining airflow predictions, while machine learning optimizes injector designs for low-emission operation. Hybrid electric-combustion systems may further decouple combustion stability from turbine load demands.
Gas turbine combustion chambers remain a focal point for advancing energy efficiency and sustainability. By integrating zonal airflow strategies with novel materials and manufacturing techniques, engineers continue to push the boundaries of combustion science. For detailed technical specifications, refer to authoritative sources such as (gas turbine fundamentals) and (NASA’s combustor classifications).
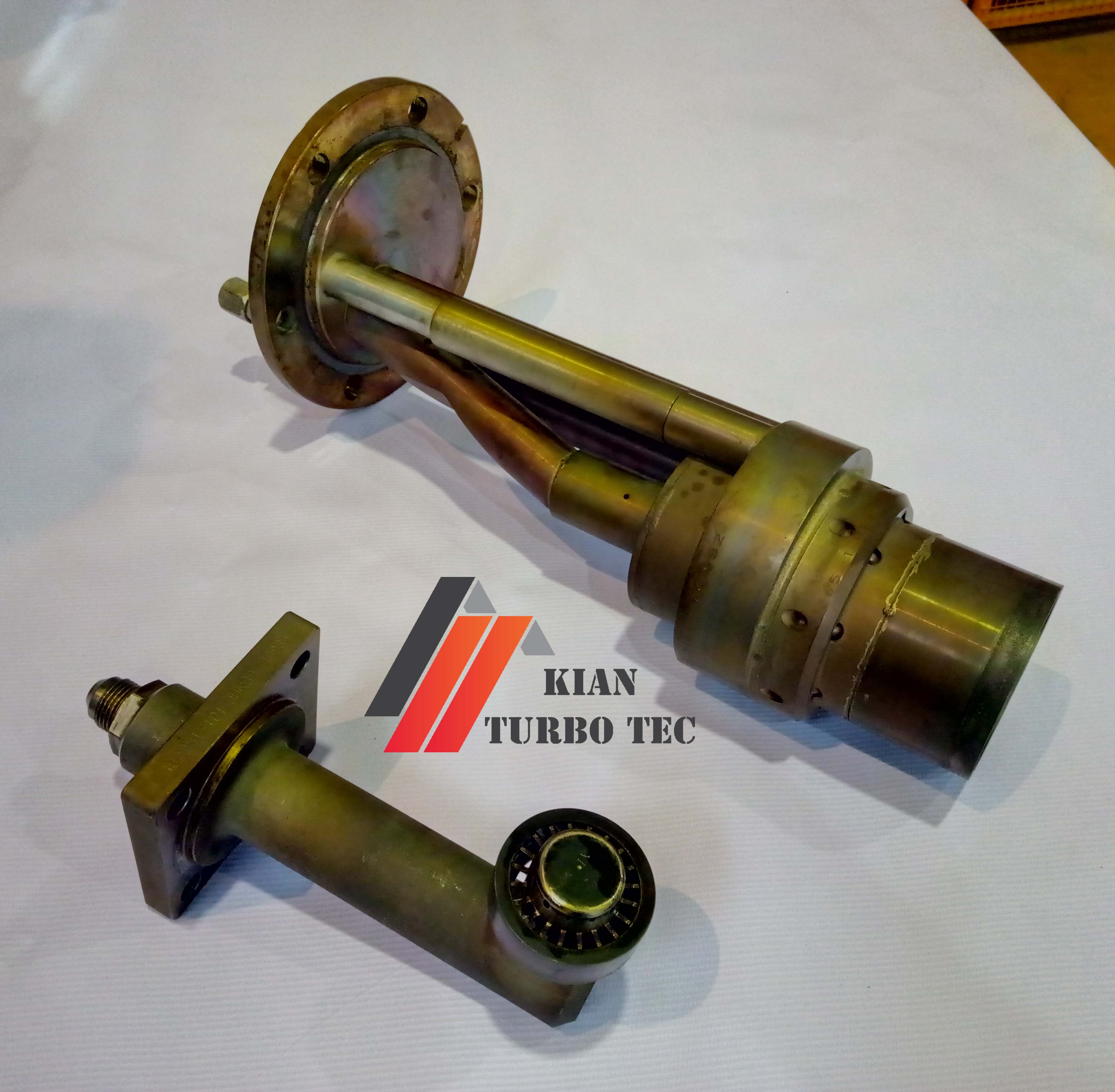
Figure 3 Fuel Injector of Taurus 70 Gas Turbine, Overhauled in Kian Turbo Tec Workshop
FAQs About Gas Turbine Combustion Chambers
1. What is a gas turbine combustion chamber?
A gas turbine combustion chamber is a critical component in a gas turbine engine where air and fuel mix and combust to produce high-temperature gas. This gas then expands through the turbine to generate power.
2.How does a gas turbine combustion chamber work?
In a gas turbine combustion chamber, compressed air is mixed with fuel and ignited. The high-pressure combustion gases produced by this process drive the turbine blades, converting thermal energy into mechanical energy.
3. What types of gas turbine combustion chambers are there?
There are primarily two types of gas turbine combustion chambers:
– Can Combustion Chambers: Individual combustion units that can be serviced or replaced independently.
– Annular Combustion Chambers: A continuous ring design that provides better mixing and combustion efficiency.
4. What materials are used in gas turbine combustion chambers?
Gas turbine combustion chambers are typically made from heat-resistant alloys, such as nickel-based superalloys. They may also feature thermal barrier coatings to protect against high temperatures and oxidation.
5. What is the role of the combustion chamber in gas turbine efficiency?
The combustion chamber directly affects the efficiency of the gas turbine engine. An optimized design ensures complete combustion, maximizing energy output while minimizing emissions.
6. What are common issues faced by gas turbine combustion chambers?
Common problems include coking, thermal stress, and erosion due to high temperatures, leading to reduced efficiency and potential mechanical failure.
7. How is the performance of a gas turbine combustion chamber tested?
Performance testing involves measuring combustion efficiency, emissions levels, and overall pressure drops using specialized diagnostic equipment and sensors.
8. What are the maintenance requirements for gas turbine combustion chambers?
Regular maintenance includes visual inspections, cleaning to remove deposits, and replacing worn components to ensure optimal performance and reliability.
9. Can vaporized fuel improve gas turbine combustion?
Yes, using vaporized fuel can enhance combustion efficiency by facilitating better mixing with air, leading to a more complete and efficient combustion process.
10. How does temperature affect the performance of a gas turbine combustion chamber?
Higher temperatures in the combustion chamber can increase efficiency but also pose risks for material degradation and necessitate advanced cooling technologies to maintain system integrity.
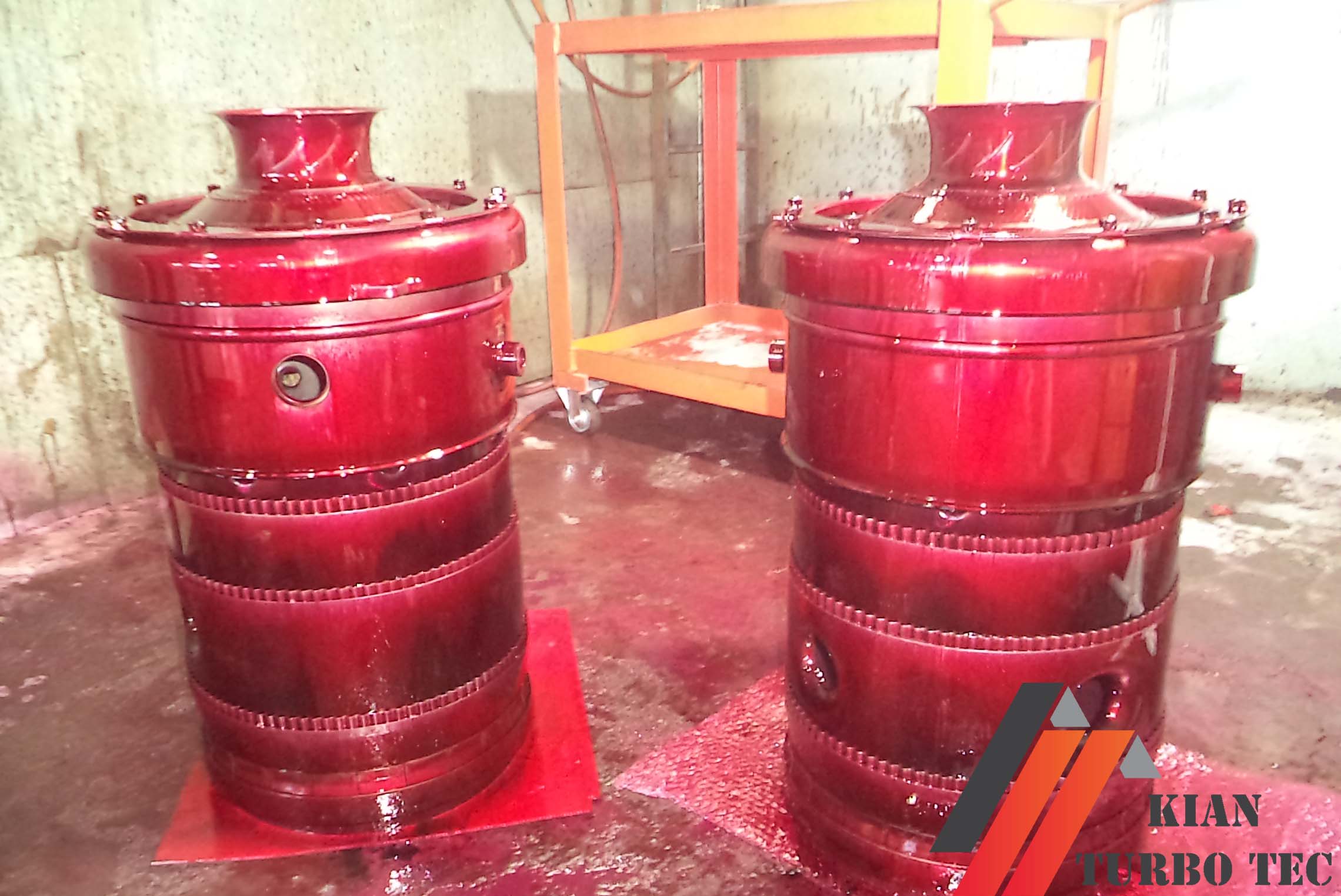
Figure 4 PT inspection of MAN THM 1304 Combustion Liners in Kian Turbo Tec Workshop