Understanding Compressor Overhaul
Understanding Compressor Overhaul: Importance, Process, and Best Practices
At Kian Turbo Tec, we specialize in comprehensive gas turbine Compressor overhauls that restore efficiency and performance. Our experienced team utilizes advanced techniques and quality materials to ensure your compressors operate smoothly and reliably. Reach out to us for tailored solutions that meet your gas turbine maintenance needs
Introduction
A compressor overhaul is a comprehensive maintenance procedure designed to restore the functionality and efficiency of a compressor, whether it’s used in industrial applications, refrigeration, or air conditioning systems. Regular overhauls are essential for preventing unexpected failures, reducing downtime, and extending the lifespan of the equipment. This article outlines the importance, process, and best practices for conducting a successful compressor overhaul.
What Is a Compressor?
A compressor is a mechanical device that increases the pressure of gases by reducing their volume. Compressors are widely used in various industries, including HVAC systems, refrigeration units, and power generation. There are several types of compressors, including reciprocating, rotary screw, centrifugal, and diaphragm compressors, each serving specific applications.
What is a Gas Turbine Compressor?
A gas turbine compressor is a crucial component in a gas turbine engine that is responsible for increasing the pressure of incoming air before it enters the combustion chamber. By compressing the air, the compressor enhances the overall efficiency of the turbine, enabling better fuel combustion and maximizing energy output. Typically designed as either axial or centrifugal compressors, these devices play a vital role in the performance and functionality of various applications, including power generation and aviation.
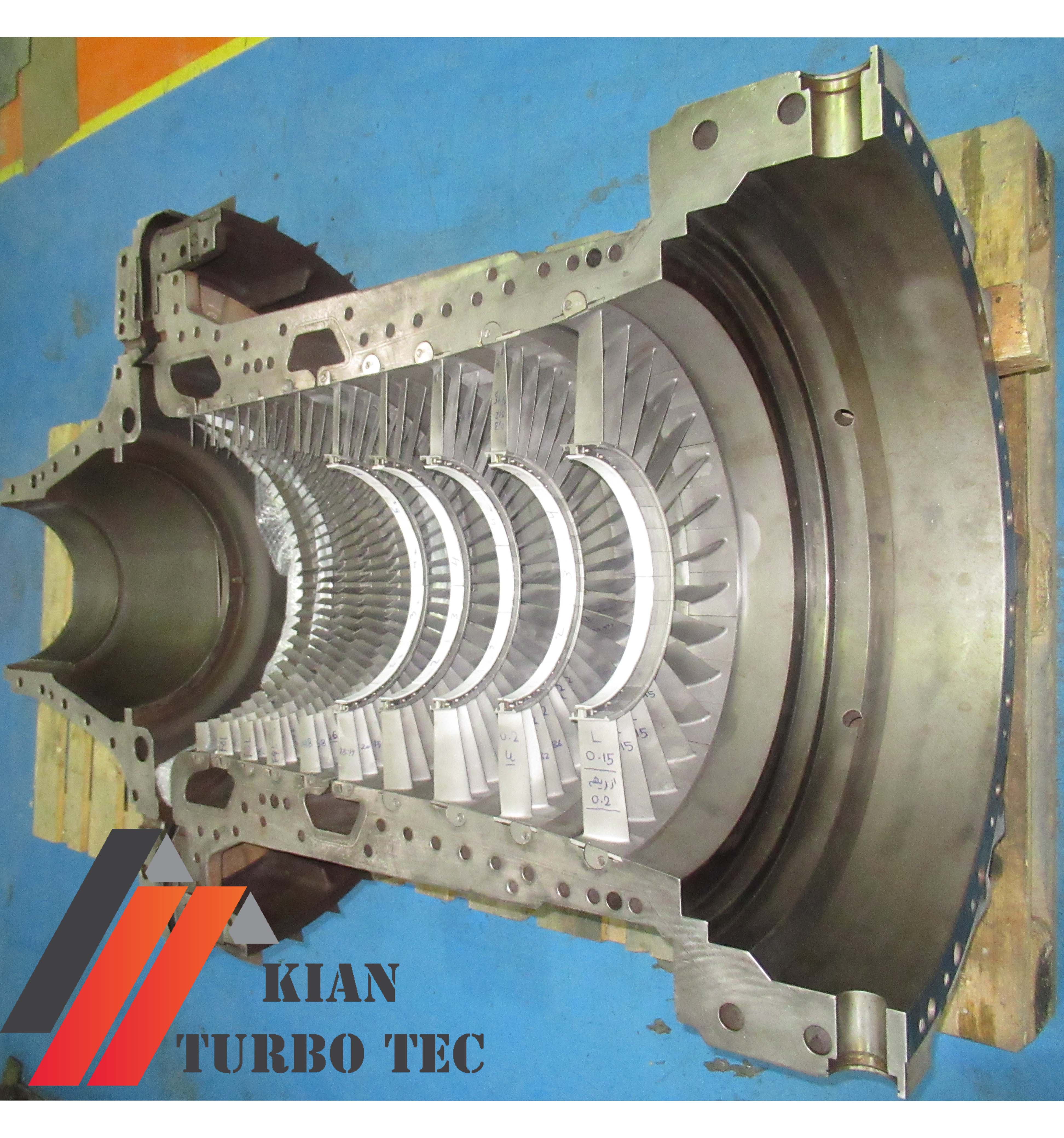
Figure 1 Inside of a THM 1304 Gas Turbine Compressor Casing, Overhauled in Kian Turbo Tec workshop
Why Is a Compressor Overhaul Necessary?
- Performance Efficiency: Over time, compressors can suffer from wear and tear, leading to reduced efficiency. An overhaul restores optimal performance levels, ensuring that the compressor operates at its intended capacity.
- Cost Savings: Regular overhauls can prevent more costly repairs and replacements down the line. By identifying and addressing issues early, businesses can save money on emergency repairs and unnecessary energy costs.
- Prolonging Equipment Life: Just like any machinery, compressors require maintenance to function properly. Overhauls can significantly extend the lifespan of the equipment.
- Preventing Downtime: Unscheduled breakdowns can lead to costly downtime. By conducting scheduled overhauls, companies can ensure continuous operation and productivity.
- Compliance and Safety: Overhauling compressors ensures they meet safety standards and regulatory requirements, minimizing risks associated with equipment failure.
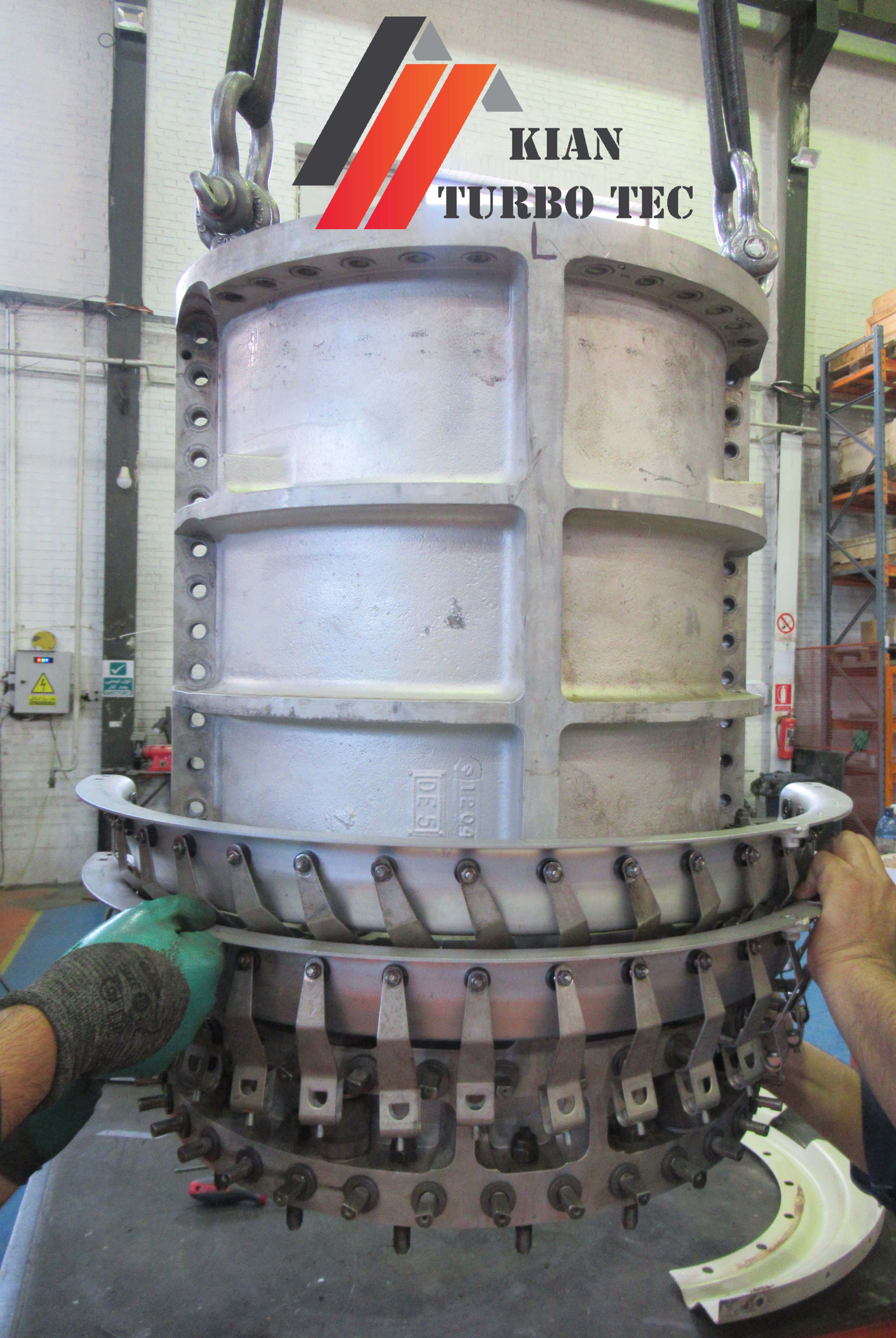
Figure 2 Solar Centaur 50 Gas Turbine Compressor Casing, Overhauled in Kian Turbo Tec workshop
Gas Turbine Compressor Overhaul Process
The compressor overhaul process typically involves several key steps:
1. Assessment and Planning
Before any work begins, a thorough assessment of the compressor’s condition is crucial. This involves:
– Data Collection: Review operating logs and maintenance records to identify patterns or recurring issues.
– Visual Inspection: Conduct a visual inspection for any apparent signs of wear, damage, or leakage.
– Performance Testing: Use diagnostic tools to test performance levels and identify specific areas that require attention.
2. Disassembly
After assessing , the next step is the disassembly of the unit. This includes:
– Disconnecting Power Supply: Ensure that it is safely powered down and disconnected to prevent accidents.
– Dismantling Components: Carefully take apart the compressor, noting the arrangement of parts for reassembly. It’s essential to keep track of smaller components to avoid loss.
3. Cleaning and Inspection
Once disassembled, each component must be thoroughly cleaned and inspected:
– Cleaning: Use appropriate cleaning solutions to remove contaminants, oils, and debris from the parts.
– Inspection: Check each part for wear, damage, or corrosion. Components such as pistons, valves, and seals are critical for the compressor’s performance.
4. Replacement of Worn Parts
Identify any parts that are worn beyond acceptable limits and replace them with new components. Common parts that may need replacement include:
– Valves
– Seals and gaskets
– Bearings
5. Reassembly
After all necessary repairs and replacements are made, it is reassembled. Ensure:
– Follow Manufacturer Specifications: Use the original assembly procedures and torque specifications provided by the manufacturer.
– Quality Checks: Double-check all connections, seals, and gaskets to prevent leaks.
6. Testing
After reassembly, the compressor must be tested to ensure proper operation. This involves:
– Performance Testing Check for correct pressure levels, flow rates, and energy consumption.
– Leak Testing: Inspect for leaks in the system, ensuring that all joints and seals are intact.
7. Documentation
Finally, document the overhaul process, including:
– Parts Replaced: Keep a detailed record of any components that were replaced.
– Testing Results: Note the performance metrics after the overhaul.
– Maintenance Schedule: Set reminders for the next scheduled maintenance or overhaul.
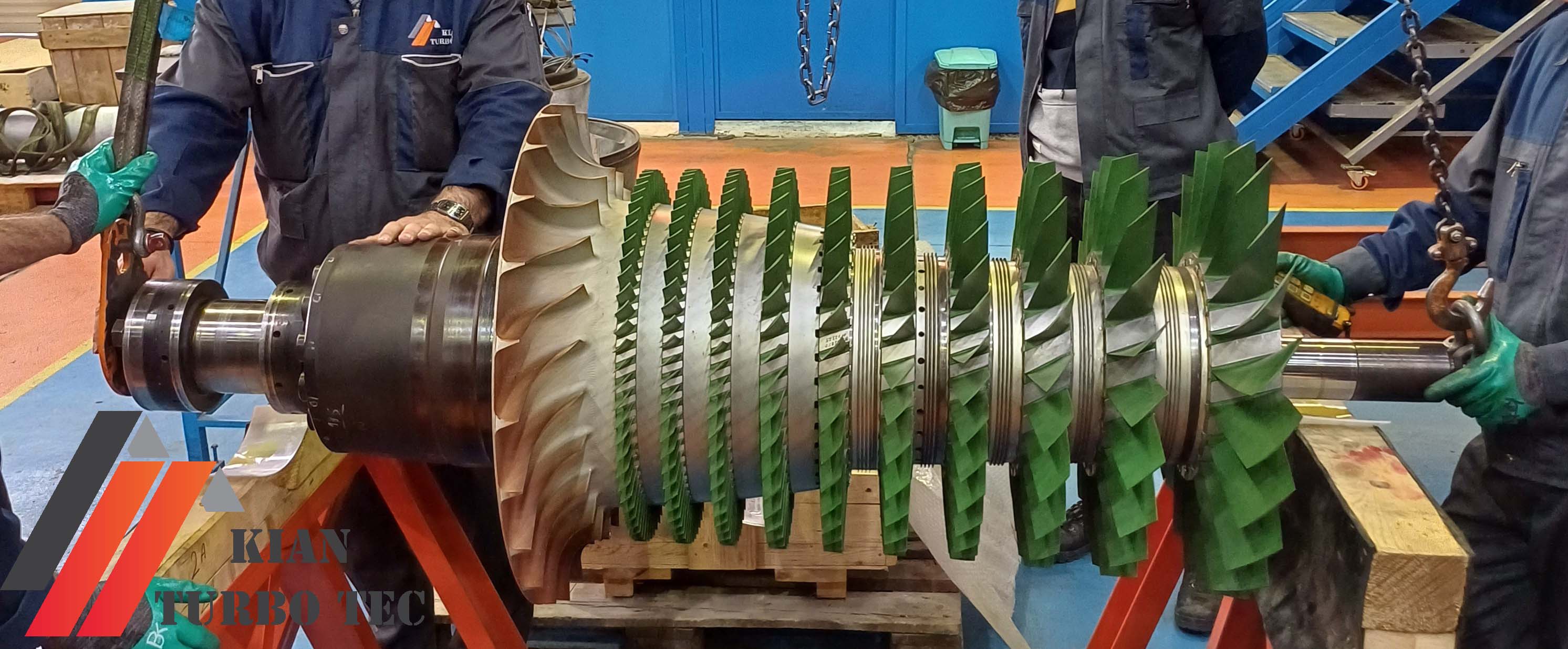
Figure 3 MAN THM1304 Compressor Rotor overhauled in Kian Turbo Tec Workshop
Best Practices for Compressor Overhaul
- Follow Manufacturer Guidelines: In Kian Turbo Tec we always adhere to the manufacturer’s recommended maintenance schedule and specifications to ensure optimal performance.
- Use Quality Parts: In Kian Turbo Tec we always Invest in high-quality replacement parts to ensure reliability and longevity in compressor performance.
- Training and Expertise: In Kian Turbo Tec we always Ensure that personnel performing the overhaul are adequately trained and experienced in handling compressor systems.
- Regular Maintenance: In Kian Turbo Tec we Implement a proactive maintenance program to monitor compressor conditions and address minor issues before they escalate into major problems.
A well-executed compressor overhaul is essential for maintaining the efficiency and reliability of compressor systems. By understanding the overhaul process and adhering to best practices, businesses can maximize the lifespan of their equipment, reduce operational costs, and ensure compliance with safety standards. Regular maintenance and timely overhauls contribute to the long-term success of any operation relying on compressor technology.
FAQs
1. How often should a compressor be routine checked?
The frequency of overhauls depends on the manufacturer’s guidelines and the operating conditions. Generally, compressors should be routine checked every 3,000 to 8,000 hours of operation.
2. What are the signs that a compressor needs an overhaul?
Signs include unusual noises, decreased performance, higher energy consumption, and frequent breakdowns.
4. What happens during a compressor overhaul?
An overhaul includes disassembly, cleaning, inspection, replacement of worn parts, reassembly, and thorough testing of the unit.
5. What are the benefits of regular compressor maintenance?
Regular maintenance leads to improved efficiency, reduced downtime, cost savings, and prolonged equipment life.