Gas turbine vane
Gas turbine vane
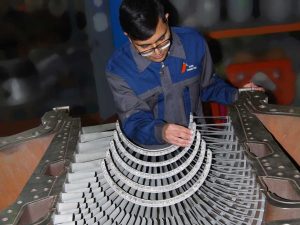
How Gas turbie vanes Work:
- Directing Flow: Vanes are positioned strategically to ensure that the hot gases enter the turbine blades at the optimal angle for maximum energy extraction.
- Optimizing Pressure and Velocity: They help to control the pressure and velocity of the gases, which is important for efficient turbine operation.
- Reducing Turbulence: By smoothing the flow of gases, vanes can help to reduce turbulence and improve the overall efficiency of the engine.
Types of Vanes:
- Inlet Guide Vanes (IGVs): These vanes are located at the entrance to the turbine stage and control the flow of gases entering the turbine.
- Variable Geometry Vanes (VGVs): These vanes can be adjusted to change the flow characteristics of the gases, allowing for better engine performance and control.
Materials and Design:
- Heat-Resistant Materials: Vanes are typically made from materials that can withstand extremely high temperatures and pressures, such as nickel-based superalloys or ceramic matrix composites.
- Aerodynamic Design: The shape and design of vanes are carefully optimized to ensure efficient gas flow and minimize losses.
Materials and Design of Gas Turbine Vanes
Gas turbine vanes are crucial components that guide hot, high-velocity gas flow within the turbine section, converting its kinetic energy into mechanical power. Due to the extreme operating conditions, the selection of materials and design features are critical for vane performance and durability.
Materials:
1. Superalloys:
- Nickel-based superalloys: These are the most common materials for gas turbine vanes due to their excellent high-temperature strength, creep resistance, and oxidation resistance. Examples include:
- Inconel 718: A precipitation-hardened alloy with good strength and oxidation resistance.
- Rene 80: A high-strength, oxidation-resistant alloy with improved creep resistance.
- CMSX-4: A single-crystal superalloy known for its exceptional high-temperature strength and creep resistance.
- Cobalt-based superalloys: These alloys have good high-temperature strength and corrosion resistance. Examples include:
Stellite 6B: A hard, wear-resistant alloy with good oxidation resistance. - Iron-nickel-based superalloys: These alloys offer a good balance of properties, including high-temperature strength, oxidation resistance, and cost-effectiveness. Examples include:
- A-286: A precipitation-hardened alloy with good high-temperature strength and oxidation resistance.
2. Ceramics:
- Silicon carbide (SiC): This ceramic material is known for its high-temperature strength, wear resistance, and low thermal conductivity.
- Silicon nitride (Si3N4): Offers excellent thermal shock resistance and high-temperature strength.
- Ceramic matrix composites (CMCs): These materials combine the high-temperature strength and wear resistance of ceramics with the toughness of metals.
3. Thermal barrier coatings (TBCs):
- Zirconia (ZrO2): Applied to the surface of the vane, TBCs reduce the temperature experienced by the underlying metal, extending its life.
Design Considerations:
1. Cooling:
- Internal cooling: Passages are designed within the vane to circulate cool air, minimizing the temperature of the vane metal.
- External cooling: Air is blown over the vane surface, creating a protective layer of cool air.
2. Aerodynamic Efficiency:
- Vane profile optimization: The shape of the vane is designed to guide the gas flow efficiently, maximizing power output.
- Trailing edge design: The shape and geometry of the trailing edge is optimized to reduce drag and increase efficiency.
3. Structural Integrity:
- Stress analysis: The vane is analyzed for stress and strain under operating conditions, ensuring structural integrity.
- Fatigue resistance: The material and design are chosen to resist fatigue and prevent cracking.
Cooling method of Gas turbine vanes
Challenges and Advancements
Gas turbine vane technology is continually evolving to meet the demands for higher efficiency, longer operational life, and lower emissions. Some key challenges include:
- Material Fatigue and Creep: Over time, vanes can experience material degradation due to the constant thermal and mechanical stresses they endure. Advanced materials and coatings are being developed to extend the lifespan of these components.
- Environmental Impact: Higher efficiency designs often operate at higher temperatures, which can lead to greater emissions. Advances in vane technology help balance efficiency gains with emissions control.
- 3D Printing and Additive Manufacturing: The use of advanced manufacturing techniques, including additive manufacturing, is being explored to produce more complex cooling channels and geometries that were previously difficult or impossible to fabricate.
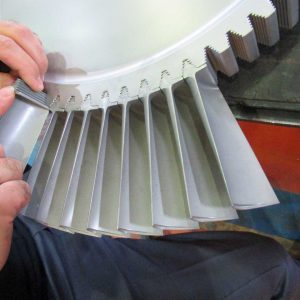
Management and Maintenance of Gas Turbine Vanes to Extend Service Life
Gas turbine vanes play a critical role in the overall performance and efficiency of gas turbines, which are essential for power generation, aviation, and various industrial applications. Due to the extreme operating conditions they face—exposure to high temperatures, pressure, and mechanical stresses—turbine vanes are vulnerable to wear, fatigue, and degradation over time. Proper management and maintenance of these vanes are vital to ensure their longevity and to maximize the operational efficiency of the turbine.
1. Importance of Maintenance for Gas Turbine Vanes
The lifespan of gas turbine vanes is primarily influenced by factors such as thermal cycling, oxidation, and material fatigue. Effective maintenance practices can significantly reduce the risk of failure, prevent costly repairs, and improve the overall reliability of the turbine. Given that turbine vanes operate at temperatures exceeding 1,000°C in some cases, maintaining the integrity of these components is critical for sustaining high performance and efficiency.
2. Inspection and Monitoring
Routine inspections and monitoring of gas turbine vanes are essential in identifying early signs of wear or damage. Advanced non-destructive testing (NDT) techniques, such as ultrasonic testing, eddy current inspection, and X-ray imaging, can detect cracks, erosion, and material degradation without damaging the components. By regularly inspecting vanes for signs of surface wear, oxidation, or cracking, operators can plan necessary repairs or replacements before catastrophic failure occurs.
3. Cleaning and Protection
Regular cleaning of turbine vanes is necessary to remove contaminants, such as carbon deposits or debris, which can cause damage or reduce efficiency. Moreover, applying protective coatings, such as thermal barrier coatings (TBCs) or anti-oxidation coatings, can significantly extend the life of the vanes by protecting them from high-temperature oxidation, corrosion, and thermal shock. These coatings act as a shield, allowing the vanes to withstand harsher operational conditions.