Commissioning Gas Turbine
Commissioning Gas Turbine Installing a gas turbine in this power plant, in addition to increasing productivity, will bring many financial benefits by reducing environmental pollution and saving maintenance and support costs.
Because the power of a gas power plant is varied, they are used to supply electricity due to the size of the network; Thus, in small and medium networks, they are used as a base load generator and in large networks as a medium load generator and peak load.
A Gas turbine is a specialized rotating engine that has the ability to extract and produce the desired energy from a fluid.
Gases, steam and water turbines usually have a protective cover around their blades that is responsible for fluid control. Covers and blades can have different geometric shapes, each of which has differences depending on the type of turbine and its application or the type of fluid and efficiency.
Solar Taurus are comprised of Solar Turbine parts, gas turbine overhaul , field service, flexible service agreements, digital solutions. and technical training in addition to remote web based monitoring and predictive diagnostic capabilities
Key steps in the commissioning process
Step | Description |
---|---|
1 | Review of turbine design and operating specifications |
2 | Tests and inspections |
3 | Start-up of turbine |
4 | Bring turbine to operating speed |
5 | Testing under load |
6 | Fine-tuning of turbine performance |
Common problems encountered during commissioning
Problem | Cause | Solution |
---|---|---|
Turbine does not start | Faulty fuel supply, ignition system, or control system | Inspect and repair the faulty components |
Turbine fails to reach operating speed | Faulty bearings, seals, or compressor vanes | Inspect and repair the faulty components |
Turbine vibrates excessively | Improper alignment, unbalanced rotor, or loose components | Align the turbine, balance the rotor, or tighten the loose components |
Turbine overheats | Faulty cooling system | Inspect and repair the cooling system |
How to start a gas turbine:
Different systems can be used to start the initial system of a gas turbine. The design and implementation of a gas turbine start-up system can vary depending on the type of turbine or the client’s order.
Many existing Gas Turbine Overhaul use an electric motor to start the turbine. This electric motor is powered by mains or adjacent units and gradually increases the speed of the gas turbine. When the permissible speed is reached, the fuel valve is opened and the ignition is activated inside the combustion chamber or chambers at the same time. By creating a flame and transferring thermal energy to the turbine, this part begins to produce mechanical work.
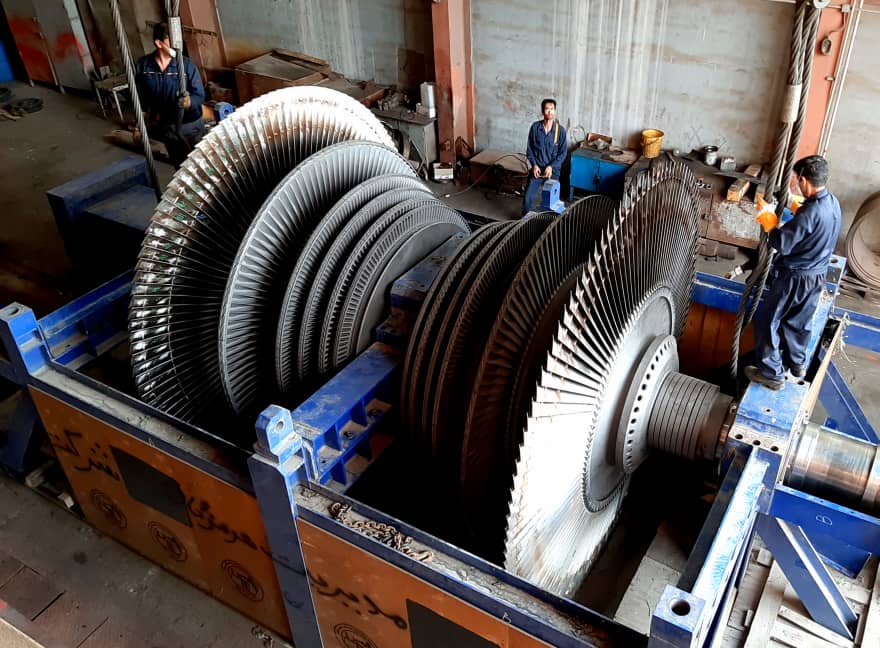
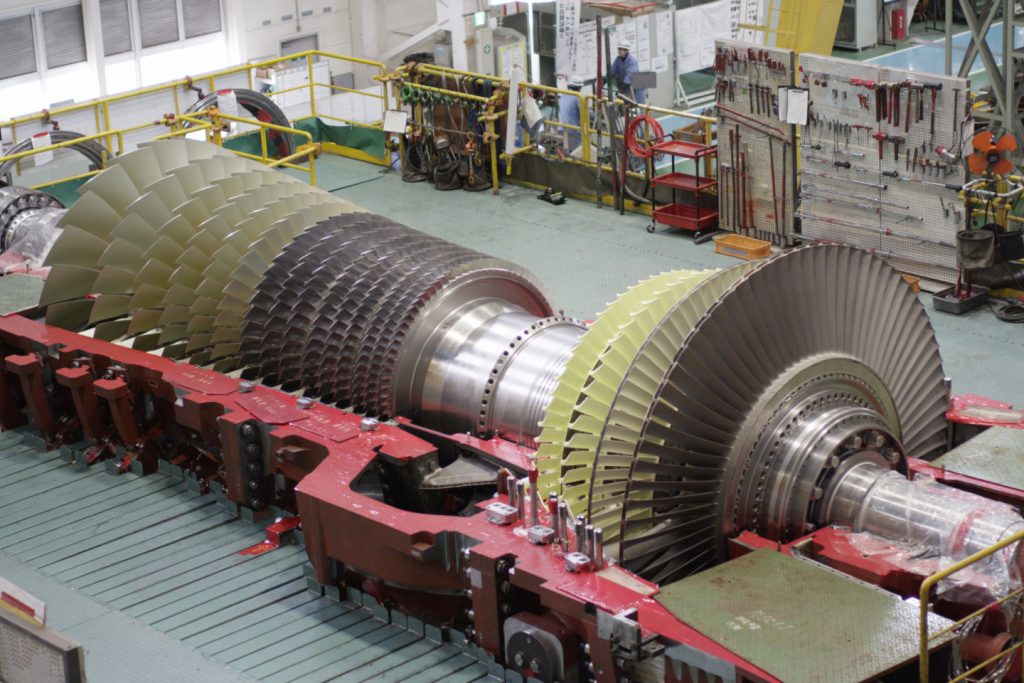
Gas turbine repair steps
Gas turbines are complex machines that require careful commissioning to ensure they operate safely and efficiently. The commissioning process typically involves the following steps:
Pre-commissioning checks: This includes inspecting the gas turbine for damage and ensuring that all components are installed correctly.
System checks: This involves checking the functionality of the gas turbine’s systems, such as the compressor, combustion chamber, and turbine.
Functional checks: This involves running the gas turbine at different speeds and loads to test its performance.
Acceptance tests: This is the final step in the commissioning process, where the gas turbine is tested to ensure it meets all performance requirements.
The commissioning process can be complex and time-consuming, but it is essential to ensure the safe and reliable operation of the gas turbine. By following the steps outlined above, you can help ensure that your gas turbine is commissioned correctly and meets your expectations.
The commissioning process
The commissioning process typically begins with a review of the turbine’s design and operating specifications. This is followed by a series of tests and inspections to ensure that the turbine is in good condition and meets all safety requirements.
The next step is to start up the turbine and bring it to its operating speed. This is done gradually, with careful monitoring of the turbine’s performance. Once the turbine is at its operating speed, it is then tested under load.
The final step in the commissioning process is to fine-tune the turbine’s performance and ensure that it is operating at its optimum efficiency.
Gas engine power plants today are built from a few hundred kilowatts to two hundred megawatts. The gas plant is placed on the chassis as completely as possible in the factory and then transferred to the installation site. The installation of the gas power plant is very fast and its commissioning speed is very high.
Other examples of supplied parts are MAN THM Gas Turbine Compressor statory and rotary Blades. It is worth mentioning that in addition to supplying parts, two of them have been majorly repaired, installed and commissioned in this company.
The advantages of the gas power
The advantages of the gas power plant include the simplicity of its turbine and its location on one axis. cheapness due to low equipment, fast installation, fast commissioning, small number of personnel, small and no need for water (except cooling and washing). Low efficiency, environmental pollution and short life. (due to wear of turbines and compressors) are also disadvantages of gas power plants.
Solar gas turbine , Among renewable energies, the sun, as an endless source of energy, has always been in the focus of researchers. The use of solar radiation energy in conventional power generation systems. such as gas turbines can play an important role in reducing fuel consumption and environmental pollution.